外観検査とは?目視とAIとルールベースと...、導入事例を交えて違いを解説
........
- 更新日
- 2025.01.28
- 公開日
- 2023.12.04
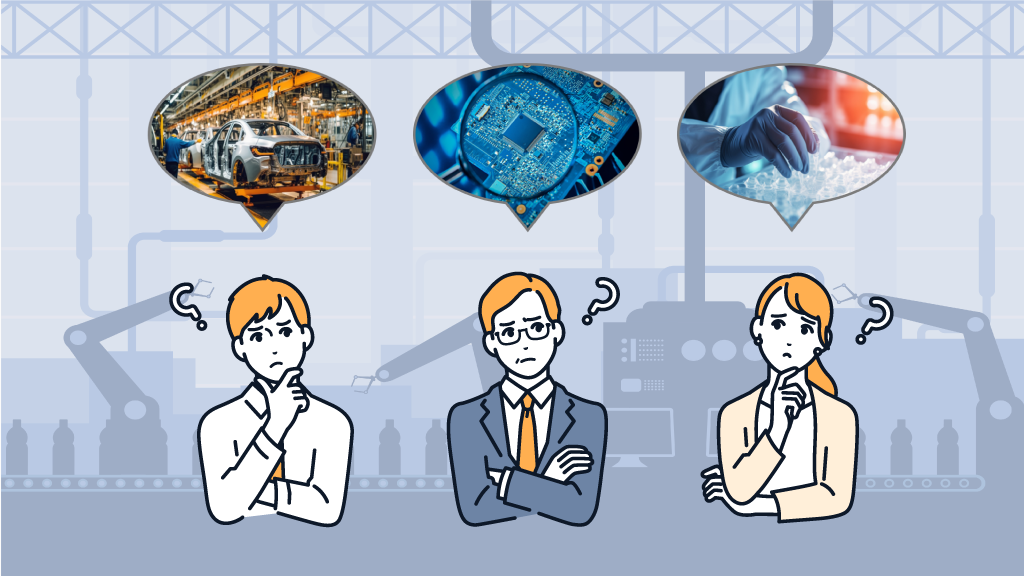
最近導入が進んでいる外観検査、検討されたことはありますか?一口に外観検査といっても色々な方法があります。外観検査の自動化が進む業界・検査方法や検査自動化の手法について見ていきましょう。
INDEX
1. 目視検査と外観検査の違いとは?
目視検査と外観検査は、どちらも製品や部品の状態を確認するための検査方法のことを指します。しかし、その範囲や手法に違いがあります。
目視検査
目視検査は人間の目で直接確認して、不具合や異常を判断する、外観検査の一種です。人間が検査するため自動化が難しい作業工程においても柔軟に対応することが可能です。しかし長時間の作業は作業者の疲労を引き起こすためミスが増えたり、人により精度やスピードにばらつきが生じる可能性があります。
外観検査
外観検査はカメラやセンサなどを用いて自動化し、製品や部品の外観を検査して不良や異常を確認する作業です。機械やAIを活用して精度と効率を高めた検査方法のため、高速で検査可能で大量生産に適しています。しかし導入するにあたり、コストがかかります。
2. 外観検査のメリットとは?
まずは、外観検査のメリットについてご紹介します。
1)省人化
技術力の高い検査員を複数確保しなければならないが、人員の確保は容易ではありません。検査員の技術習得まで時間を要することや、特定の検査員に負荷が集中するような事態を防げます。
2)検査工数・費用の削減
複雑な検査項目を自動化することで、検査工数を削減し、業務を効率化できます。たとえ不具合が大量発生した場合でも、自動化していれば検査員の負担が急激に増加することを防ぐことができ、検査費用の削減にも繋がるでしょう。
3)品質の維持
目視検査は人の感覚や経験、体調などの人的要因で検査の質が変化するため、確認項目の増加や長時間の緊張状態が続くと、ケアレスミスの危険性が高まるが、外観検査を導入することで人的要因に影響されず、高い品質を維持できます。
3. 自動化が進む業界・検査方法について
外観検査を導入するためには、検査の範囲・内容・目的を明確にすることが重要です。一口に外観検査と言っても業界や検査対象によって求められる基準は大きく変化します。外観検査が進んでいる業界の特徴と検査方法についてご紹介します。
1)業界の特徴
詳細 | |
---|---|
半導体・電子部品 | マイクロチップやPCBの製造工程では、微小な欠陥も許容されず、迅速なフィードバックが必要なため、リアルタイムで高精度な検査が求められる。 |
食品・医療品 | 食料品では、食材ごとの形状の差異を考慮した異物混入や形状の欠陥を検出する必要があり、医療品では、人の目だけでは検出困難な異物や成分の違いを検出する必要がある。 |
自動車 | 車体の塗装や組み立て部品の検査では、塗りムラやキズを短時間で検査する必要がある。 |
2)検査の方法
詳細 | |
---|---|
異常・キズ検出 | 製品内部や表面に存在する微小な異物・キズを確認する。 |
形状・サイズ | 製品の形状やサイズが設計基準に準拠しているかを確認する。 |
色調・パターン | 色の均一性や印刷パターンの正確さを確認する。 |
4. 車載部品の外観検査例
車載には多くの機械部品が使用されており、部品ごとに異なる視点・粒度で検査を実施しています。下記の図では、車載部品の検査例をご紹介します。
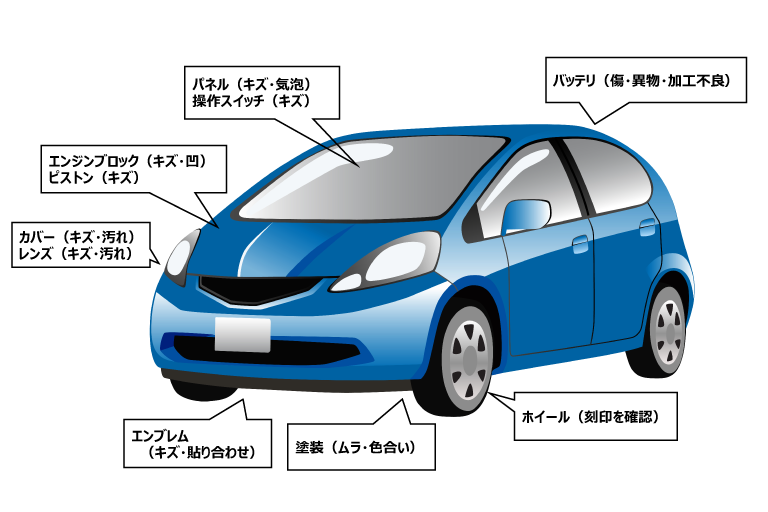
5. ルールベース検査とAI外観検査の違いや特徴とは?
外観検査、品質保証、システム動作確認などの多くの分野で自動判定が行われていますが、判定の方法は「AI」と「ルールベース」の2つが主流となっています。2つの手法はどのように異なるのでしょうか。それぞれの特徴と利点を整理しました。
ルールベース方式 | AI・教師なし学習(良品学習) | AI・教師あり学習(良品・不良品学習) | |
---|---|---|---|
概要 | 技術者がデータを元に判定アルゴリズムを作成、判定を行う | ソフトウェア(AI)がデータを元に学習モデルを生成、判定を行う | |
判定根拠 | ホワイトボックス | ブラックボックス | ブラックボックス |
必要なデータ量 | 少ない | 中程度 | 多い |
強み | 判定速度が速い、判定根拠が明確 | 良品サンプルのみでOK(サンプル集めが楽) | 柔軟かつ高い精度で判定可能 |
弱み | 良品/不良品の境界が曖昧なケースではルール作成が困難 | 良品サンプルから外れたものをNG判定するため、閾値設定が難しい | 良品・不良品のサンプルが大量に必要となるが、不良品のサンプル集めが難しい |
6. ルールベースの導入事例
検査装置(ルールベース方式)の導入事例をご紹介します。
FPC挿入検査システム(自動車向けモジュール)
項目名 | 項目 |
---|---|
導入背景 | 基板のコネクタにFPCケーブルが挿入されていることを検査員の目視にて確認していたが、今後のビジネス拡大に向けて「検査員の削減」、「検査の見逃し防止による品質向上」を目的として自動化を検討 |
作業内容 | ユーザの教育や実地検証での最適な判定ルールの提案、本番導入に向けた設置/設定のサポートを実施 |
導入期間 | 3ケ月 |
導入費用 | 約400万円 |
導入効果 | 検査の見逃しの排除による品質向上、人的リソースの有効活用 |
本件の場合は、基板のコネクタにFPCケーブルが挿入されていることを判定するということで、判定基準も明確だったためルールベース方式をご提案しました。その結果、AI方式に必要な「学習データの収集・学習モデル作成」の工数を短縮し、短期間・低予算で自動化を実現できました。
7. まとめ
お客様ごとに困りごと(人手不足、技術継承、品質担保の課題解決策など)があり、検査対象も異なります。困りごとにぴったりはまる外観検査が見つけられず、導入を断念してしまう場合もあるでしょう。当社では皆さんの困りごとをヒアリングし、コーディネートします。ぜひ、お問い合わせください。
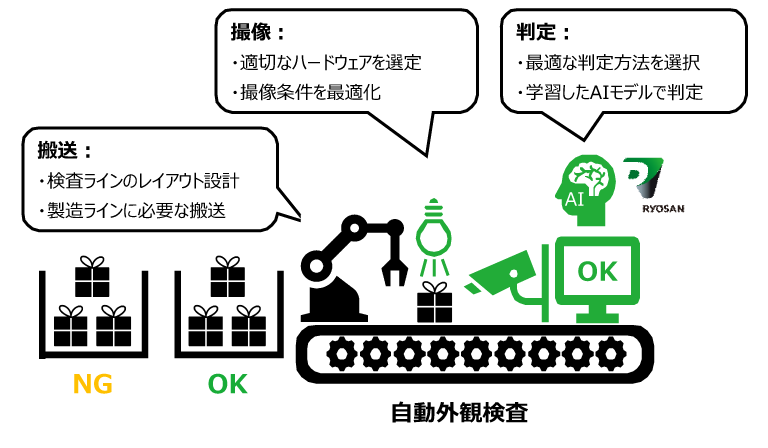