メンテナンスを変える。異常検知の動向
........
- 更新日
- 2024.05.24
- 公開日
- 2023.07.04
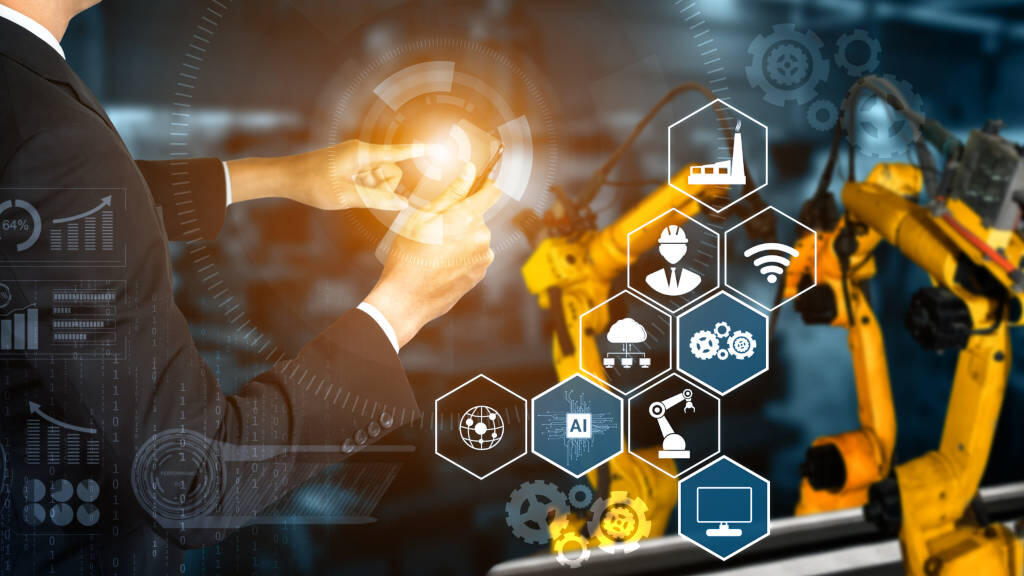
検査員の経験則に機器の異常検知を頼りすぎると、予期せぬ人員交代や検知漏れで思わぬ損失に繋がるかもしれません。機器の常時監視・状態の見える化で、スマートにメンテナンスを行いましょう。
■こんな方におすすめ:
- 機器の異常を故障前に自動で検出したい
- スマートメンテナンスのユースケースを知りたい
INDEX
1. スマートメンテナンスとは
スマートメンテナンス(予測メンテナンス)は、製造設備にセンサを設置して状態に関するデータをリアルタイムに収集・分析することで、メンテナンスの必要性を予測する仕組みです。従来型のメンテナンスは、設備の故障後に修繕する事後保全、もしくは故障の有無にかかわらず定期的に実施する予防保全を中心に行われてきました。スマートメンテナンスは、センサからの情報を活用しメンテナンスの必要性を予測することで、設備の円滑な運用を保ちつつ、設備停止により生じる修繕費用やライン停止のリスクを低減できるなど、そのメリットは大きなものです。
メンテナンスは、必要に応じて行えば最も費用対効果が高くなります。予防保全は、頻繁に設備の修理を行うため維持費がかさみます。一方、修繕が必要になるまでメンテナンスを引き延ばすと、設備の性能を一定以上に戻すためのコストがかかってしまいます。スマートメンテナンスは、収集するリアルタイムデータを基に、最適なメンテナンス時期を特定できます。
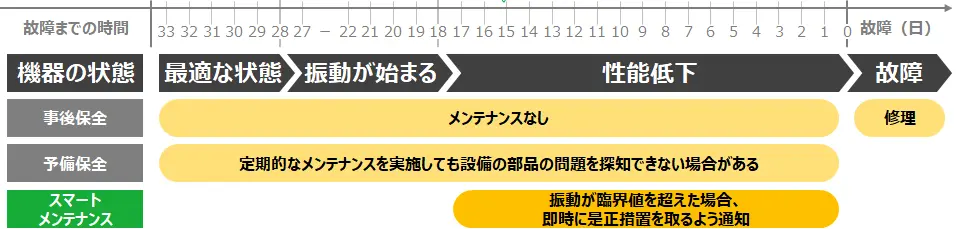
2. なぜスマートメンテナンスが必要なのか?
デジタル庁は2024年1月11日に日本の法令のアナログ的な規制、いわゆる「アナログ規制」の見直しに向け、人による“目視・見張り”を代替するデジタル製品やサービスの募集を開始していると発表しました。現在、河川法や都市公園法では、河川・ダム・公園の巡視点検業務において人が現場で目視確認することを求めています。また、道路交通法では、安全運転管理者講習において、遠方の居住者に対しても講習会場への来場を求めています。このような目視・定期検査・対面講習・実地監査・常駐と専任・書面掲示などを求めるアナログ規制について、デジタル庁はオンラインやAI・IoT・ドローンなどで代替可能な法令、約1万条項の見直しに向けた工程表を公開し、2024年6月までにすべて見直す方針を示しました。“地方公共団体におけるアナログ規制の点検・見直しマニュアル第2.0版”も公開し、見直しに取り組むための推進体制・作業手順案を提示しています。
アナログ規制の見直し状況はデジタル庁のダッシュボードで確認可能です。
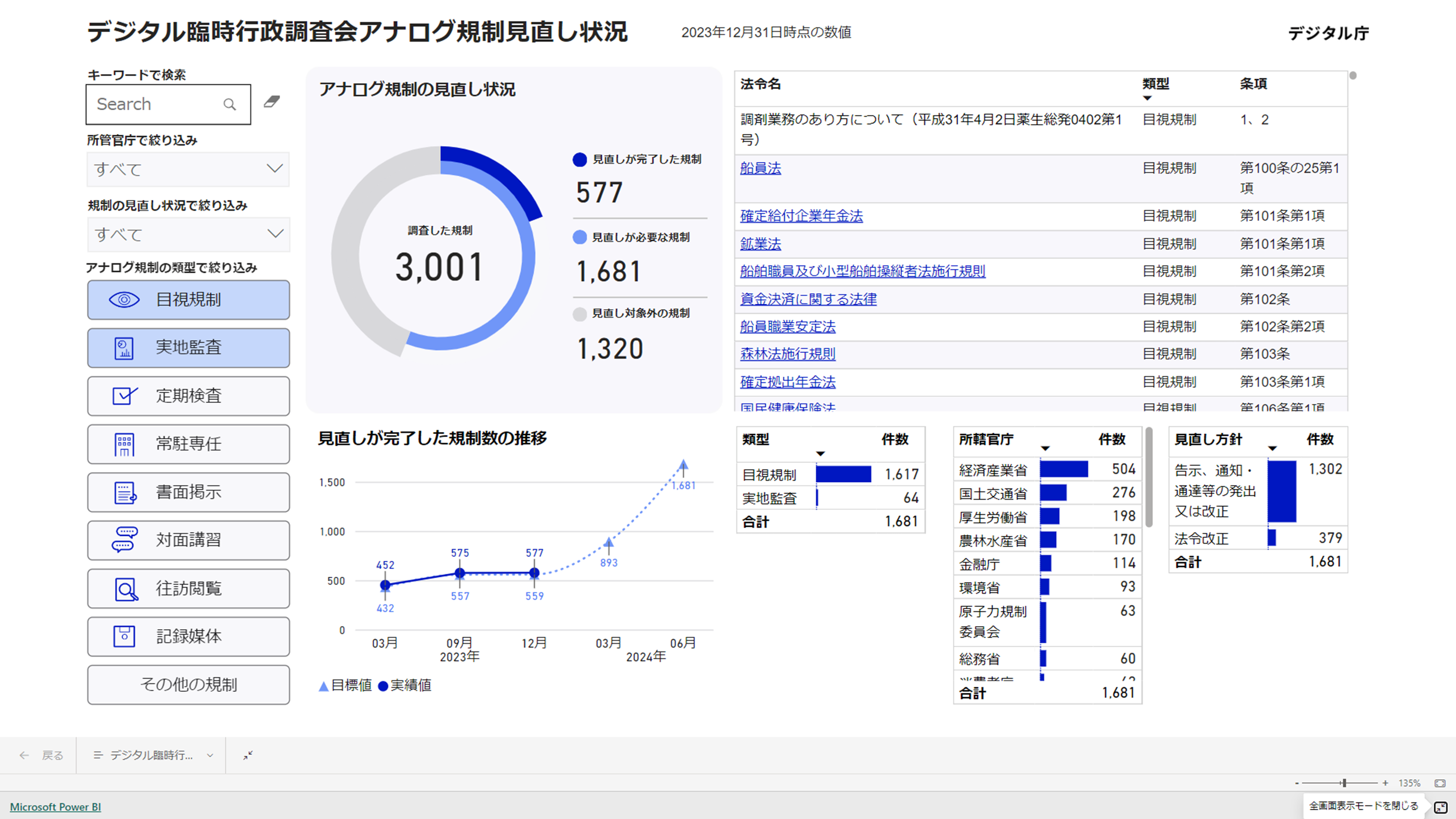
https://www.digital.go.jp/resources/govdashboard/administrative_research
さらに、2024年3月29日には“アナログ規制見直しに活用できるテクノロジーマップ・技術カタログに関する取組の試行版ページ”を公開し、規制を所管する省庁や地方公共団体に対して、デジタル技術の進展等を踏まえた自律的・継続的な規制の見直しを支援しています。
テクノロジーマップでは、技術類型を特定可能とし、特定した技術類型に関連する具体的な製品・サービスの情報を技術カタログで詳細に確認できる構成としています。具体的には、縦軸にユースケース・検査すべき内容・取得すべきデータを置き、横軸で提供される機能を置くことで、用途と機能に応じた技術(カメラ、マイク、各種センサ、ドローン・ロボットなどの機器・ツール)を確認できます。
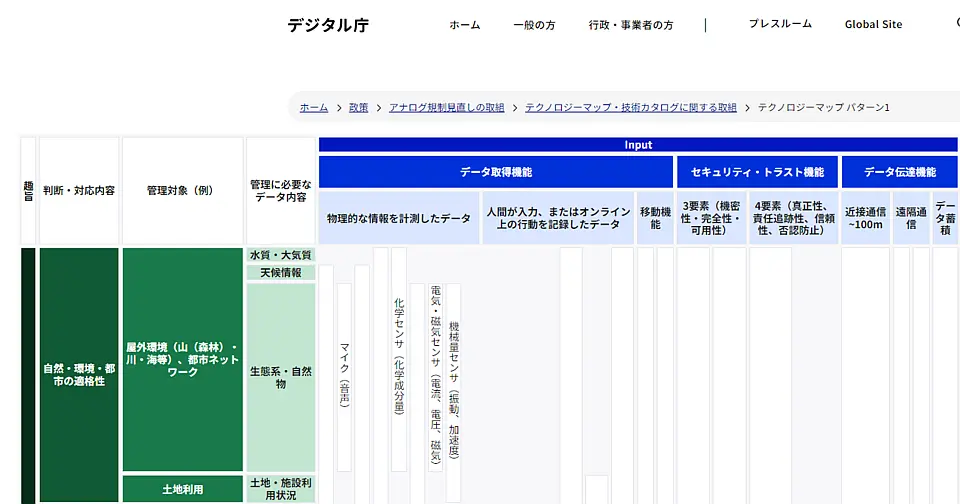
https://www.digital.go.jp/experimental/technology-map/
3. どのような状態を「異常」と判断すればいいのか?
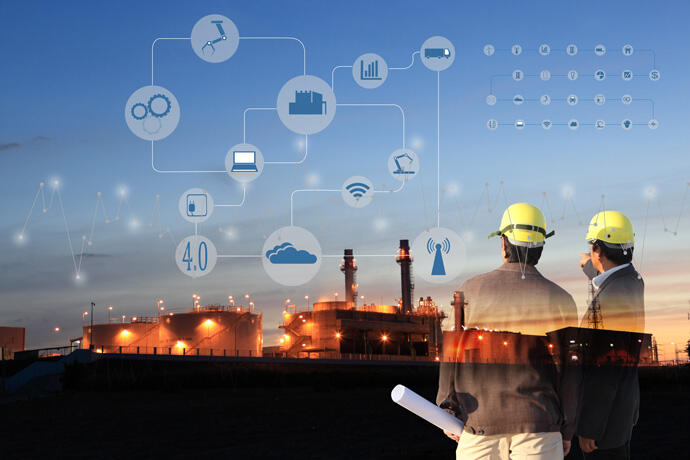
スマートメンテナンスでは、まず何を「異常」とするかを決めることが大切です。どの状態が正常で、どの状態になると異常の兆しとするのかを定義することが、自動検知を進める1stステップとなります。
例えば……
- モータの異常 → 音、振動、ひび割れ
- 設備の破損 → 振動、対象物の見た目の変化
- 機器の発熱・供給電源 → 温度、電流や電圧の上昇
- 通信障害 → 通信ケーブル劣化や断線、ノイズ干渉
モータ稼働の異常を検知するには、音や振動が監視の対象となります。物理的破損ですと、機器本体の見た目の変化を検出することが必要です。電源や熱の異常であれば、検知すべき項目は、電流・電圧などが対象になります。
見える化が進めば、生産・検査工程の効率向上による働き方改革や、機器の廃棄削減など、企業として取り組むべき課題へも効果が期待できます。
何が「異常」かが決まれば、検出手法の選定が2ndステップとなります。
どのようなユースケースがあるのか、スマート化の3つの動向をまとめましたので、課題・対策案・効果を見ていきましょう。
4. 設備検査のスマート化動向
ユースケース① 音 × AI
〇 課題
工場設備の検査手法として使用前後検査、定期検査等されている場合が多いですが、今回の工場では熟練の検査員が設備のモータ音を耳で聞いて確認する官能検査に頼っていました。当検査の課題として検査員により異常検知にバラつきがあること、後継者育成が難しいことがあります。
〇 対策案
該当設備のモータ付近にマイクを設置し、マイクで集音したモータ音をAIで解析する設備異常を検知。
〇 効果
設備の状態をリアルタイムにモニタリングし、定量的に正常・異常の判断が行える。また、検査員が現場に赴く必要がなくなりリモートで正常・異常の確認が出来るようになり、検査員の工数削減にもつながる。
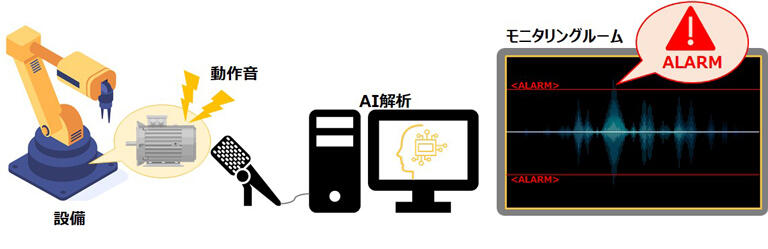
\\ 音 × AI = 製造DX //
見た目では捉えにくい問題や、故障予測に活用可能
ユースケース② カメラ × AI
〇 課題
設備オペレータは一人で複数の作業を行う多能工なので、常時モニタリングは出来ません。そのため、工場設備で突発的に起きる異常を瞬時に止める事は困難であり、且つどこに異常があるか原因の特定も難しくなります。
〇 対策案
工場設備付近にカメラを設置してカメラの撮影範囲に異常があった場合、設備オペレータや管理者などへメールで発報。
〇 効果
常時モニタリングにより、突発的な異常が起きた時にも瞬時にアラートが上がり、早期対応・原因特定が出来る。原因特定が可能となったことで、改善対策により設備の破損回避やオペレータの安全確保にも繋がる。また、定期的に設備を見に行く回数が減り、工数削減も可能。
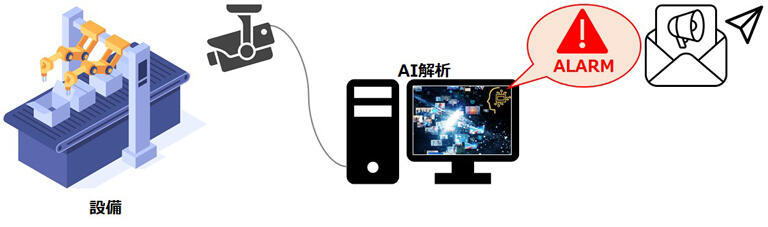
ユースケース③ 電流 × 通報システム
〇 課題
工場にある配電盤で瞬間的に漏電が起きる事があります。老朽化した設備が原因だが不定期で発生するため、最悪の場合は工場全体が停電してしまう可能性があります。そのため、漏電発生時は即時検出する必要があります。
〇 対策案
該当設備の電源部分に電流センサを後付けし、設備に流れる電流値を常時モニタリング。モニタリングシステムに連動し、異常があった場合は、管理者などへメール発報。
〇 効果
常時モニタリングと即時発報のシステムにより、監視員の巡回中も漏電に即時対応でき、漏電遮断器の作動による停電の心配がなくなる。また、監視員の複数人配置も不要となり、工数が削減できる。
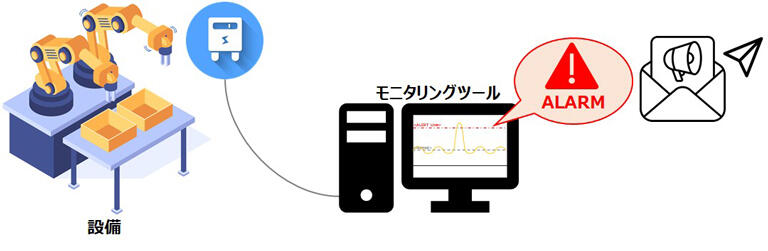
5. 異常検知に使われるデータのメリット・デメリット比較
異常検知には各種センサを使用します。使用するセンサにより取得データの内容・精度、設置方法などが変わるため、対象となる機材に合わせて異常検知の方法を検討する必要があります。下表に代表的なセンサをまとめましたので、検討の参考としてください。
製造DX、スマートメンテナンスにご興味を持っていただけましたら、是非ともご連絡ください。
6. まとめ
AIスマートメンテナンスの導入効果
✔ 対象設備の稼働状況をリアルタイムに見える化
✔ 正常・異常判断の定量化
✔ データ改ざんの抑制
✔ 検査員の負担軽減
異常検知はお客様の製品や保有している生産設備により、手法が変わります。
いきなりシステム導入をするのではなく、対象の設備で異常検知ができるか判断するため、まずは、簡易検証から進める事をおすすめします。
省人化や官能検査でお困りがございましたら、ぜひお問合せフォームよりご相談ください。
-
\\ 音 × AI = 製造DX //
-
\\ 製造DX × 予測AI = 異常予知 //