【解説】プリント基板の大電流対応と小型化を両立するバスバー
........
- 更新日
- 公開日
- 2024.07.22
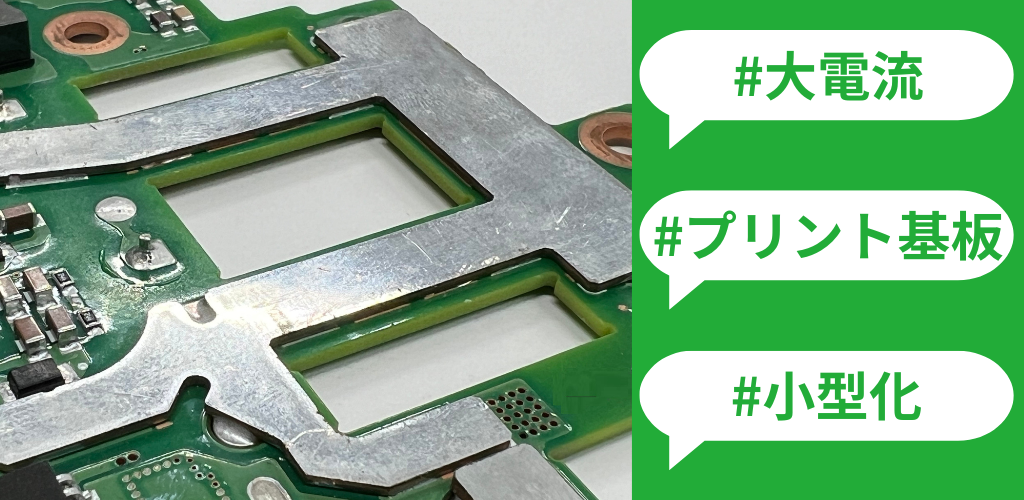
パワーエレクトロニクス分野のお客様から大電力化に伴う設計課題をお伺いすることが増えています。本記事ではパワーエレクトロニクスの市場動向と、大電力に対応するためのプリント基板関連技術をご紹介します。
1. パワーエレクトロニクスの市場動向
1. パワーエレクトロニクス市場
パワーエレクトロニクスは、電力を効率的に変換・制御するために古くから存在する技術です。身の回りの家電製品や電気自動車、太陽光発電など私たちの日常生活の中で幅広く活躍しています。近年の環境問題への対応に向けても、大電力を扱うパワーエレクトロニクスは特に注目されている分野です。
このグラフは、パワーエレクトロニクスを支える重要部品「パワー半導体」の市場規模の動向です。製品の電動化や高性能化、小型化の要求に応じてパワーエレクトロニクスが寄与できる領域が拡大しており、2035年には2023年実績の約2.5倍の市場規模となる大きな成長が見込まれています。
2. プリント基板から見たパワーエレクトロニクス市場
パワーエレクトロニクス開発動向を把握できるデータとして、弊社資本提携先の株式会社プリケン(プリント基板メーカ)の受注状況をご紹介します。株式会社プリケンでは主に試作用プリント基板の製造を行っており、近年パワーエレクトロニクス用途での受注が増えています。下のグラフは、受注案件のうちパワーエレクトロニクス用途が占める件数と金額の割合です。先ほどご紹介したパワー半導体の世界市場と同様に増加傾向が見られ、実際の開発現場でもパワーエレクトロニクス分野に注力されていることが分かります。
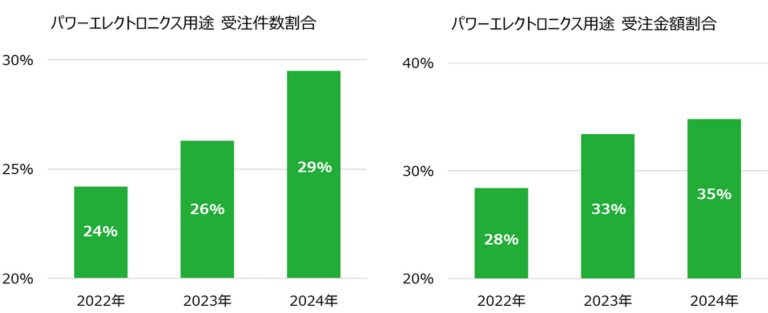
2. プリント基板の大電流対応手法と課題
パワーエレクトロニクスを用いる様々な製品では、大電力化による大電流対応の設計が求められています。例えば、電気自動車ではバッテリーの大容量化が進んだことで、従来よりも高出力なモータを搭載できるようになりました。高出力モータには多くの電力が求められ、その電力を供給する回路には大電流対応が必要になっています。
プリント基板の設計では、一般的に銅箔厚35umの場合、1Aの電流を流すために1mmの配線パターン幅が必要とされます。これを超える電流が流れると、発熱や焼き付きなどの問題を生じてしまいます。本章では、大電流を安全に流すための3種類の対応手法についてお話しします。
1. パターン幅を広げる
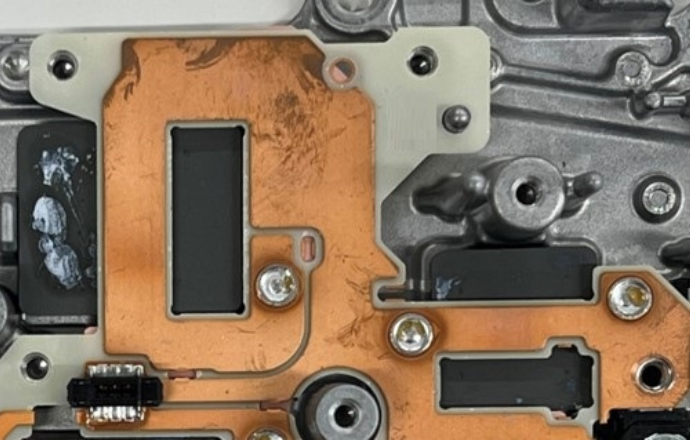
パターン幅を広げることで、大電流を流せます。上述の電流1Aに対して配線パターン幅1mmの目安から単純に考えると、50Aを流すためには50mmのパターン幅が必要になります。(プリント基板設計規格IPC-2221に準じた設計の場合は、更に広げる必要があります。)
その副作用として、電流量に比例して基板面積がどんどん大きくなってしまいます。許容スペースに収められなかったり、製品の小型化の要望には応えられないため、適用できるケースは限られています。
2. パターンの厚みを増やす
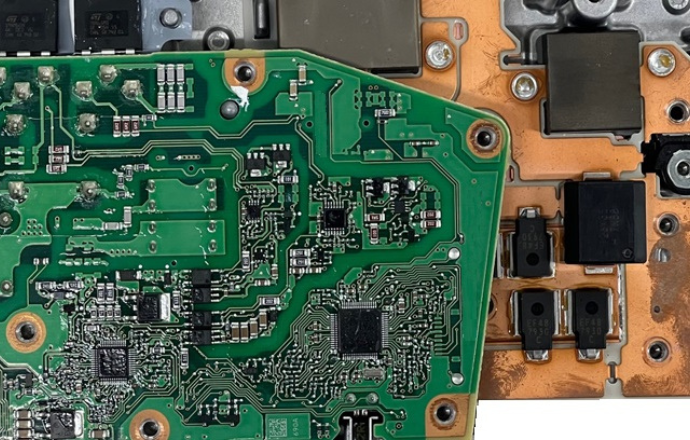
基板面積を大きくしないために、パターンの幅ではなく厚みを増やすアプローチもあります。パターンが厚く作られた基板を「厚銅基板」と呼んでいます。
標準的な製造方法で対応できる銅箔の厚みは35~70μm位ですが、厚銅基板は数百μmの銅厚のパターンを備えています。パターンの幅を広げることなく立体的にパターン体積を稼ぐことで、大電流を流せます。
基板の面積が増えないため一見魅力的な対策に見えますが、厚銅基板では基板の製造工程上、狭ピッチ対応が難しく小電力系のマイコンなどを搭載できません。結果として小電力系と大電力系(厚銅基板)の2枚の基板に分けて設計することになり、写真のような複数基板の構造になります。基板のコストアップにつながり、設計作業も複雑化してしまいます。
3. 基板の多層化
電流を流す配線層の数を増やすアプローチもあります。多層基板の内層銅箔に210~500umなどの厚みを持たせることで、大電流を複数の内層に分けて流す方法です。表面層は標準的な銅箔厚に抑えることで、厚銅基板では搭載できなかった狭ピッチ部品も問題なく搭載できます。
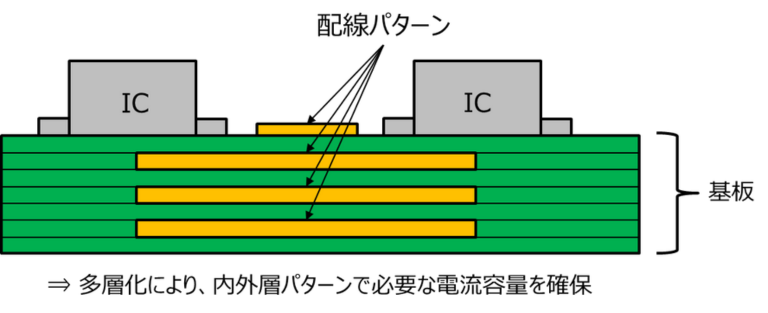
一方で、基板の多層化は製造工程が増えるため、パターンの幅や厚みを増やす対策よりもコストがかかることが問題になります。
大電流に対応するための3種類の基板対策をご紹介しました。どの方法も基板の大型化やコストアップなど新たな課題を生じるため、対応手法の即決は難しいでしょう。手法の選択に悩んだとき、これらの課題も解決できる打開策はないのでしょうか?
3. 大電流化と小型化を両立!バスバーとは?
写真の銀色の部品は、バスバー(Bus Bar)と呼ばれる部品です。銅・真鍮・アルミからなる金属部品で、基板サイズを抑えながら大電流対応を実現するキーパーツです。
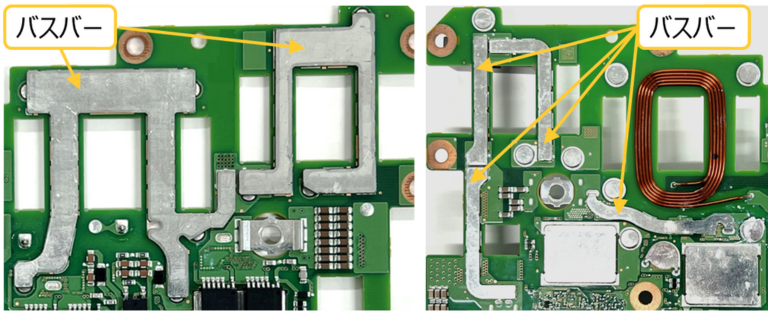
バスバーをご使用頂く場合は、下表のようなメリットをご提案できると考えています。
バスバーの特性 | お客様のメリット |
---|---|
放熱しやすい露出形状 | 表面に導体が露出している構造のため、優れた放熱性を活用できます。 |
加工容易性 | 基板形状に対する制約がないため、お客様の基板形状に合ったバスバーをご使用頂けます。 |
交換可能 | 基板変更なしでバスバーを交換できるため、複数仕様のバスバーを用いて対応電流や放熱性の比較検討が容易です。 |
リフロー対応 | 銅線を手付けする等のレガシーな放熱対策と比較して、組み立ての工数削減や品質を向上できます。 |
それでは、2章でご紹介した一般的な3種類の基板対策と、バスバーを用いる対策を比較してみましょう。
1. パターン幅を広げる
パターン幅拡幅よりも、小さな面積で大電流対応が可能です。

2. パターンの厚みを増やす
大電力系用の厚銅基板を追加する必要がなく、バスバーを実装した1枚の基板で大電流対応ができます。
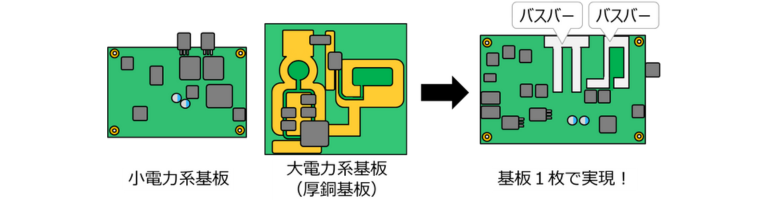
3. 基板の多層化
製造コストがかさむ多層基板を避けて、加工が容易なバスバー追加で大電流対応を実現できます。

このようにバスバーは、プリント基板での課題の打開策としてご検討頂けると考えています。
4. まとめ
パワーエレクトロニクス分野で求められている大電流対応に向けて、一般的な基板対策とバスバーをご紹介しました。プリント基板とバスバーを組み合わせることによって、従来の基板だけでは対応できなかった課題を解決できる可能性があります。大電流対応に向けて困り事をお持ちの方、バスバーでの対策に興味をお持ちの方は、弊社までお気軽にご相談ください。お客様の課題について一緒に検討させて頂くことを楽しみにしています。
(執筆者:高橋 達也、編集者:大内 崇臣)