部分最適?全体最適?製造現場を効率化するデジタルツインとは
........
- 更新日
- 公開日
- 2025.06.30
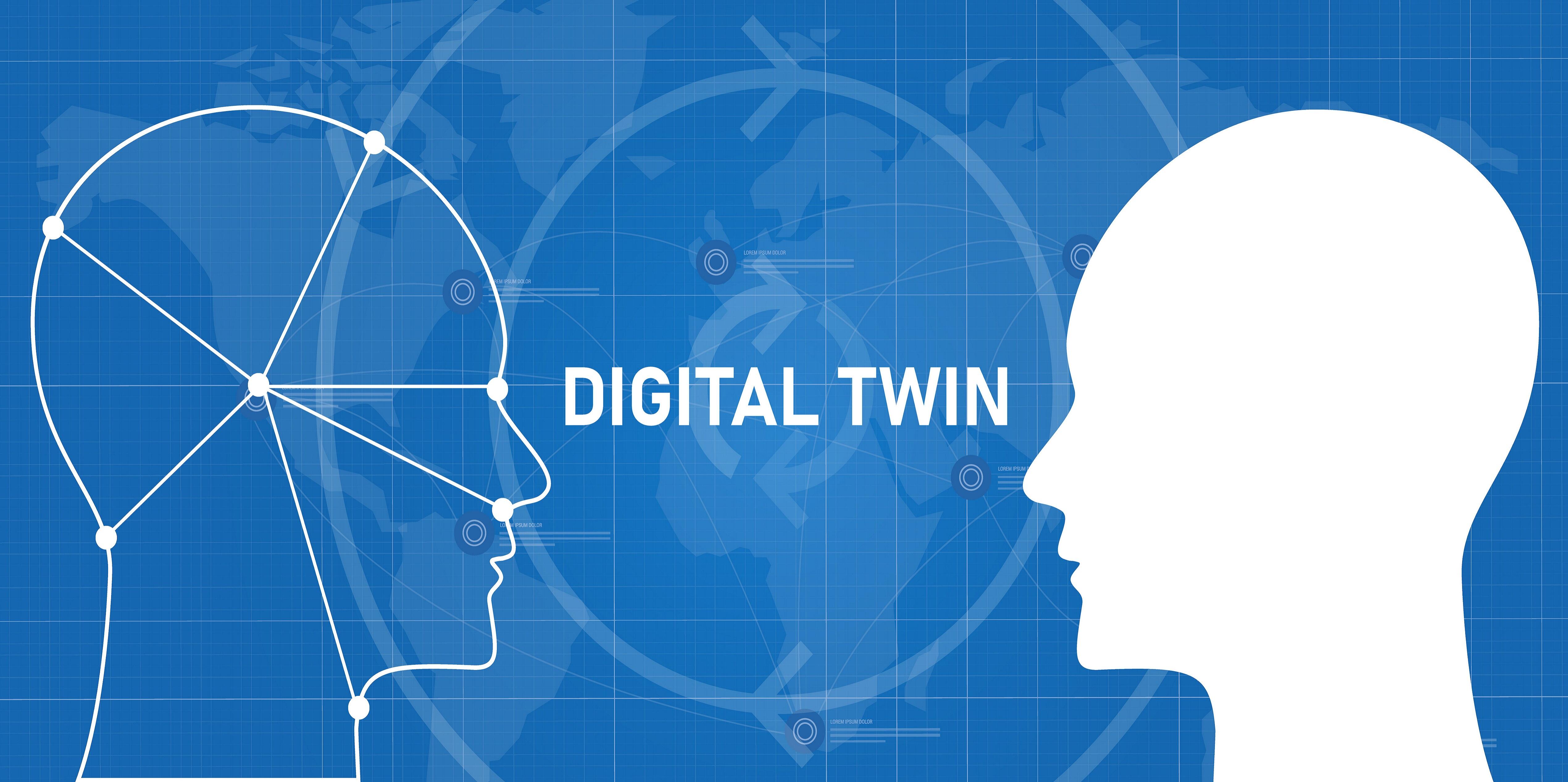
製造現場では、日々改善活動が行われており、特定の作業や工程の効率化(いわゆる部分最適)は着実に進んでいます。しかし、生産ライン全体を見渡したとき、本当に効率的な運用ができているでしょうか?
実際には、「ある工程では効率化が進んでいるものの、全体の流れとしては依然として改善の余地がある」といったケースが多く見られます。
この記事では、「部分最適」だけでなく、生産ライン全体の効率を高めるために重要な「全体最適」の重要性やその実現に欠かせない「デジタルツイン」の役割についても詳しくご紹介します。
1. 製造現場における「部分最適」の進展と限界
日本の製造業では、日々の改善活動やムダの削減、省力化などが積極的に行われており、多くの現場で作業単位や工程単位での効率化が進んでいます。これにより、生産性の向上という成果も得られています。
しかし、こうした「部分最適」だけでは、生産ライン全体のパフォーマンス向上には限界があります。たとえば、大手企業からは「ライン全体の最適化には依然として課題がある」「工場内の動線が悪く、建屋が分かれているため工程の集約が難しい」といった声も聞かれます。こうした現場改善の積み重ねを通じて、「今後は全体最適を目指す必要がある」という新たな意識が現場で広がりつつあります。
経済産業省(※1)でも、『大企業を中心に、既存の部門や業務にとどまらず、製造プロセス全体を見据えた最適化への移行が進みつつある』と指摘されています。
※1:経済産業省「製造業を巡る現状と課題 今後の政策の方向性」
※製造現場におけるAIやIoTを活用したDXの取り組みについては、こちらもあわせてご覧ください。
2. なぜ「全体最適」への転換が必要なのか
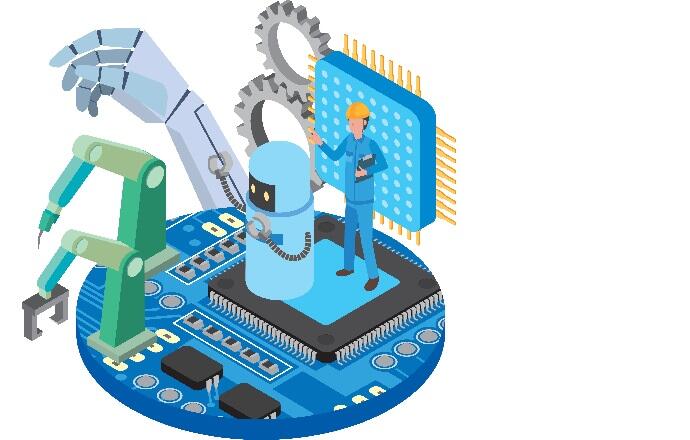
多くの現場では、省人化や省力化を目的としてロボットの導入や作業改善が進められています。しかし、ロボットの動作シミュレーションや工程分析が個別に行われているだけで、全体として十分に連携・統合されていないケースが多く、その結果、最終的な調整が難しくなることがあります。
また、シミュレーションで得られた理想的な動作が、実際の現場ではうまく機能しないこともあります。仮想空間で検討した理想的な動作が、現場にそのまま適用できず、再度調整が必要となるため、時間やコストが余計にかかる「揺り戻し」が発生します。
こうした課題から、「部分最適の積み上げでは限界がある」「プロセス全体を見据えた製造ラインの設計・運用が必要だ」という考えが広がりつつあります。
3. マクロ環境の変化と製造業への影響
製造業を取り巻く環境は、かつてないほど複雑で不安定になっています。自然災害、国際紛争、パンデミックなどの予測不能な出来事が、サプライチェーンの寸断や操業停止といったリスクを引き起こしています。
さらに、日本では少子高齢化による労働力不足が深刻化しており、現場の人材確保がますます困難になると予想されます。加えて、カーボンニュートラルなど脱炭素への対応も急務となっています。これらの要因によって、製造現場では管理コストや運用負荷が増加しています。
このような背景からも、既存の部門機能・業務を前提とした「部分最適」ではなく、開発から設計、調達、生産、出荷、保守までのものづくり全体のプロセスを視野に入れた「全体最適」への転換が求められています。
(デジタル技術を用いて、ものづくりの全体プロセスを最適化する手法については、以下(※2)が参考になります。)
※2:国立研究開発法人 新エネルギー・産業技術総合開発機構「スマートマニュファクチャリング構築ガイドライン」
4. 全体最適の鍵「デジタルツイン」とは?
4-1. 一般的なシミュレータとデジタルツインの違い
「デジタルツイン」とは、現実世界の建物や道路などのインフラ、経済活動、人の流れなどをリアルタイムでデジタル空間に再現し、シミュレーションや最適化を行う技術です。従来のシミュレータと異なり、現実と仮想が常に連動している点が特徴です。
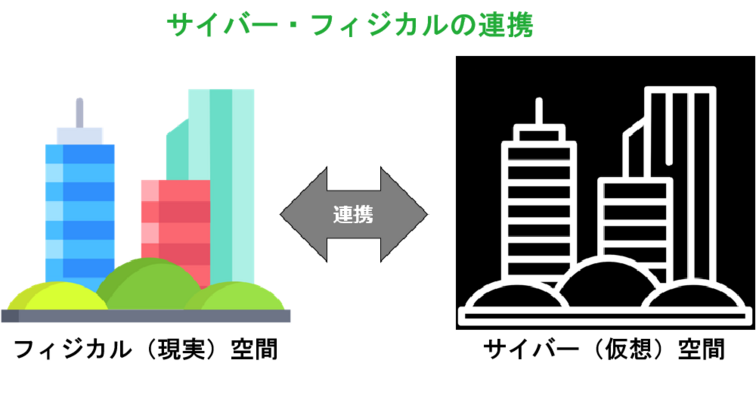
デジタルツインには、目的や対象に応じて、様々なスケールのものが存在します。
4-2. 製造業におけるメリット
製造業では、開発から出荷までの全工程を仮想空間で再現・分析できるため、現実とのギャップを最小限に抑えられます。設計変更や需要変動の影響も事前に評価できるため、迅速な意思決定や柔軟な対応が可能となります。
複雑化する製造現場において、デジタルツインは「全体最適」を実現するための有力な手段です。DX(デジタルトランスフォーメーション)の中でも、デジタルツインは中心的な役割を担うと考えられています。
5. デジタルツイン導入の課題
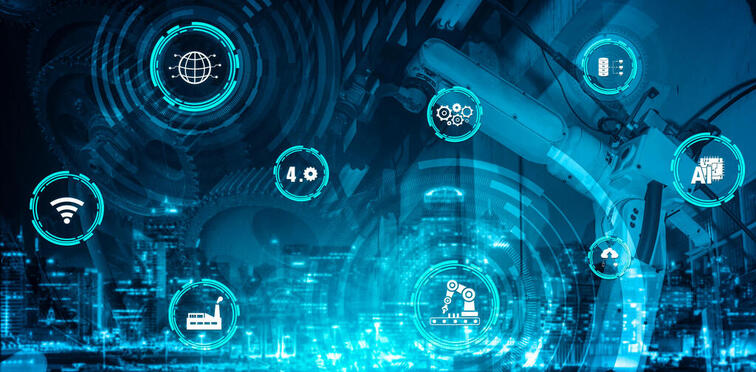
デジタルツインの導入には多くのメリットがありますが、課題も存在します。特に大きいのが導入・運用コストです。リアルタイムデータを収集するIoT機器や、データを分析・処理するAIシステムの導入が必要となります。
また、膨大なデータを管理し、現実に近い仮想空間を維持するための運用コストも無視できません。導入を検討する際は、コストと効果を十分に見極めたうえで、必要な技術を持つ人材の確保やシステムの整備が重要です。
6. まとめ
本記事の要点を以下にまとめます。
- ロボットやシミュレーションの導入による部分最適は進んでいるものの、工程全体の最適化は依然として不十分
- デジタルツイン技術により、現実と仮想空間を連携させた全体最適が可能
- デジタルツイン導入にはコスト面や技術面での課題があり、慎重なシステム構築が求められる
本記事の内容が、少しでも皆さまのお役に立てれば幸いです。
(執筆者:江田 昌隆 / 編集者:宮崎 研一)